See it. Say it. Sorted (or is it?)
- Elizabeth Coggins-Hill
- May 21, 2019
- 4 min read
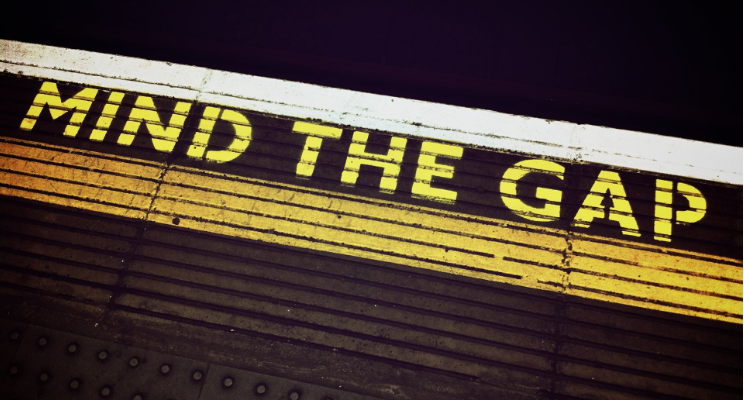
If you’ve been to the UK, and anywhere near a train or a Tube station in the last year, you will probably have heard this slogan aimed at getting the public involved in with reporting suspicious items and preventing terrorist acts. Indeed, the phrase has become a bit of a meme with a life of its own. When I heard it recently on a train in London, it got me thinking about the phrase in different contexts. What if I removed the bomb/terrorist threat and put in place a more mundane one?
I have seen many companies over the years from heavy engineering, assembly, design offices, consultants, architects, freight forwarding, shops and so on. In many cases the staff at the “coal face” relied on the concept of “See it. Say it. Sorted.” to keep their area running, by passing problems or decisions up the chain of command or to specialist departments for resolution. Why?
Lack of trust that staff might know what they are talking about?
Lack of skills to analyse and address the problem?
Lack of encouragement to address the problem?
Hostile environment in which to experiment with solutions?
It might be any one or a combination of the above.
I remember one site visit where I noticed a lack of a barrier on a loading ramp. On closer inspection it turned out that two of the brackets for the crash barrier had been bent out of shape so that the two bars could no longer be held in place. I asked the manager, who asked the ramp supervisor who asked the guy responsible for the barriers, and we received the answer “we reported it to Purchasing and asked them to buy two more brackets”. The very busy people in Purchasing found the request, the order had been placed, but nobody had followed up on the delivery. Health & Safety had a note of the missing barrier in its book, but no one had followed it up. So, where was the failure? It appeared to a systemic one, one muddied by unclear responsibilities, priorities and worst of all: assumptions. What to do?
See it
Never underestimate the power of a picture! We taught the guys on the ramp to “see” and document the issue and risk in a structured way. That means taking pictures to illustrate the point and thinking of the consequences of inaction. Pinning the pictures to the team board made sure that they weren’t forgotten in the course of day-to-day business. Stop if the risk was critical.
Say It
We provided them with the tools and the training to “say” in a structured manner so that all in the process knew what the issue was and what was expected of them in order to assist the team in resolving it. This enabled the issues to be tracked in a standard manner.
Sort it.
We trained them in tools such as A3, 8D, Process Mapping and Practical Problem Solving with root cause analysis. We encouraged 5S, Autonomous Maintenance and Standard Work. We gave them the ownership of resolving issues in their area and let them experiment in improving flow and reducing risk. The Dispatch Department was re-framed as one of the most important elements in ensuring Flow to the customer, with the administrative functions as support roles.
6 months later:
The Dispatch Area was unrecognisable. I was stunned to see the pride and eagerness with which the changes were explained to me. The site manager was in the process of implementing a site-wide Lean transformation touching every aspect and involving everybody. The Dispatch Department showed how they had devised a traffic light system to signal to Production which parts and pallets were stuck in “Safe Launch Inspection” and risked missing the daily shipment to the customer. They had successfully pushed Finished Goods Inspection back into Production.
12 months later:
The number of parts going through “Safe Launch Inspection” had reduced dramatically, as Production found it disruptive to keep pulling people off lines to check work that should have been done properly in the first instance. They had put their own improvements in place and were working much closer with their adjacent functions. Administrative functions focused on resolving their parts in enabling Flow. It was the first company site in its European division with:
an on-site customs-controlled warehouse
locking bay doors if the truck didn’t have chocks under its tyres and a host of other safety features
a speed camera linked to the site security office to slow traffic, flag bad drivers and identify repeat offenders
number-plate recognition to allow vehicles onto the site
18 months later:
A forklift-free production with amazing visible flow and an enviable safety record. Everyone to whom I spoke knew what their part in the whole was and what to do if something were amiss. Flow and Safety were in the forefront of everybody’s mind with Lost-time accidents a thing of the past.
The Plant Manager told me of his and the Supply Chain Manager’s corporate conference trip to the US where out of all the Managers they were the only ones not on the phone to his plant every break. They had a system in place and trusted the team to address the day-to-day issues, knowing that if something catastrophic arose they could reach them.
They went from “See it. Say it. Sorted (or not)” to “See it. Say it. Sort it.” It was a team effort with strong positive leadership, defined expectations, training at all levels, space and encouragement to experiment, and a clear vision that everyone bought into. That’s the power of good Lean implementation.
After all, everyone deserves to go home safe at the end of the day.
Comments