
PAST PROJECTS
PARTS STRATEGY
Germany
Elizabeth Coggins-Hill was engaged to review the current parts processes and design strategy and initiatives, with focussing on:
-
Inventory & Materials Management & process flow
-
Global Process standardisation
-
Driving cross-functional collaboration
-
Driving internal and external change in a matrix organisation
Following a period of data gathering which included process and material flow mapping, system data evaluation, with local teams, we defined 3-year strategy for Inventory & Material flow improvements and agreed upon a framework for implementation of “Plan for every Part” according to Toyota Production System. The first benefit came from implementing inter-plant service level agreements and re-assessing production locations, which saw a €0.5m reduction in pipeline inventories.
INVENTORY REDUCTION
Germany, Italy, Slovenia, Spain, Turkey, Poland, UK & Sweden
Facing a cash-flow challenge, the client requested me to review productive inventories and implement projects where improve opportunities could be identified. The initial step was to develop a company-specific Inventory Reduction roadmap to assist in identifying potential areas for reduction. Once over 200 individual projects were identified, these were ranked and a reporting mechanism for improvements developed. Elizabeth Coggins-Hill was responsible for overseeing the local implementation teams in 8 countries, coaching, and for escalating or resolving issues. The projects included:
-
MRP System review
-
Master Data cleaning
-
Capacity Planning adjustment
-
VMI / Consignment Stock
-
Pack-size adjustment
-
Delivery frequencies
-
Re-alignment of off-site warehousing
-
Move-to-pull
as well as cross-department collaboration in sourcing, IT and engineering. In the course of one year a sustained inventory reduction of £8.5m was achieved, with a further £1.6m in cost-avoidance logged, while parts sales increased by 10%.
MATERIAL FLOW
Turkey
A manufacturing location facing a significant expansion and site reorganisation requested my assistant in providing a “guiding hand” for the Supply Chain function. The changes included a completely new traffic lay-out, moving to fork-lift-free production, a customs-controlled area, and three new manufacturing cells. Elizabeth Coggins-Hill worked with the team to:
-
Design a safe and efficient material flow, with a coherent site-flow concept including reverse-material
-
Map the storage and material flow onto the production system
-
Secure on-time delivery of the project
She also provided mentoring and coaching in lean principles, team management and safety; regular process reviews; as well as escalation and dispute resolution, where necessary.
Interested in a free call?
How about a no-strings, confidential 45-minute call to talk through your current Supply Chain situation?
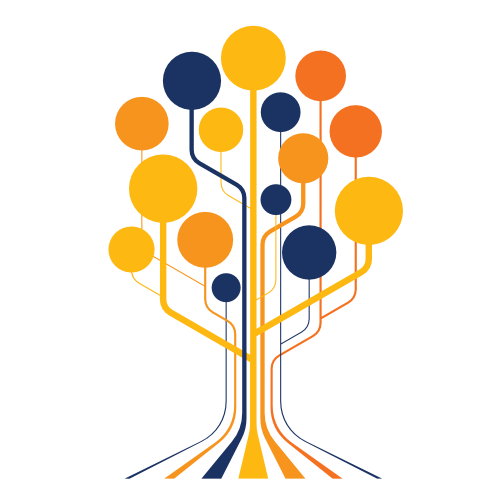